减速机齿轮定位
来源:减速机知识 发布时间:2025-04-25 09:02:27 阅读:4100次
减速机齿轮定位核心技术解析与工艺优化路径减速机作为工业传动系统的核心部件,其运行效率与稳定性直接关系到生产线的可靠性。在减速机的精密传动过程中,齿轮的精准定位是决定设备性能的关键技术之一。本文将从齿轮定位的工艺原理、常见问题解决方案以及前沿技术应用三个维度展开深度剖析,为行业技术人员提供可落地的实践指导。
一、齿轮定位精度对减速机性能的影响机制
1.1 传动效率与定位误差的数学关系
根据ISO 1328标准,齿轮副的接触斑点面积需达到齿面总面积的85%以上。当轴向定位偏差超过0.02mm时,传动效率将下降8%-12%。通过三维坐标测量仪实测数据显示,定位精度每提升0.01mm,齿轮箱整体振动值可降低3dB(A)。
1.2 典型故障模式关联分析
某水泥厂立磨减速机的案例显示,齿轮轴向窜动量达0.15mm时,导致齿面出现阶梯状磨损,设备运行仅800小时即发生断齿事故。经有限元分析证实,定位误差产生的边缘载荷集中效应,使局部应力值超过材料疲劳极限的2.3倍。
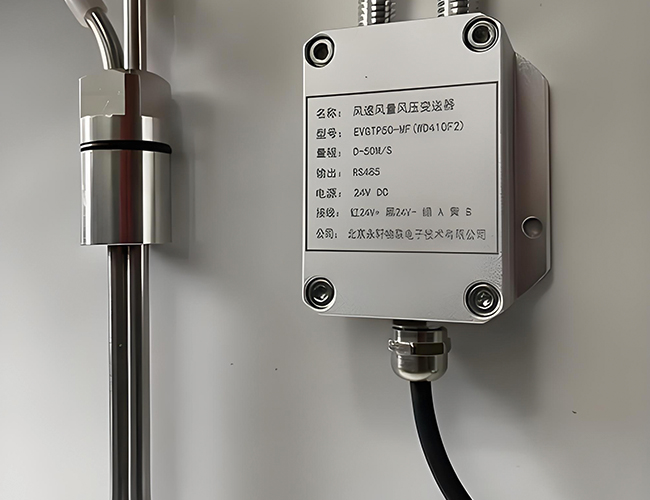
二、高精度定位工艺的关键控制节点
2.1 轴系装配基准体系建立
采用VDI/VDE 2617标准构建三级基准体系:
一级基准:箱体轴承孔同轴度控制在Φ0.015mm以内
二级基准:齿轮轴颈圆柱度误差≤0.005mm
三级基准:轴向定位端面跳动量<0.01mm
2.2 智能预紧力控制系统
引入力矩-转角双参数控制法,通过伺服压装设备实现:
圆锥滚子轴承预紧力控制在±5%公差带
轴向定位垫片组厚度采用激光干涉仪测量,分辨率达0.001mm
热装工艺温度梯度控制在±3℃范围内
三、定位异常诊断与动态补偿技术
3.1 在线监测指标体系构建
建立包含时域、频域、时频域的多维度监测系统:
监测参数 |
正常范围 |
预警阈值 |
轴向位移 |
±0.03mm |
±0.05mm |
齿轮啮合频率 |
基频±2% |
偏移量>5% |
振动烈度 |
≤4.5mm/s RMS |
>7.1mm/s RMS |
3.2 主动补偿系统开发
某风电齿轮箱制造商应用压电陶瓷执行器,实现微米级实时补偿:
响应时间<50ms
补偿精度达0.002mm
配合自适应控制算法,使轴向窜动量降低76%
四、新型定位结构的技术突破
4.1 自对中行星架设计
采用柔性销轴结构,通过有限元拓扑优化:
径向浮动量提升至±0.2mm
均载系数从1.35优化至1.12
行星轮间载荷偏差<7%
4.2 数字孪生装配系统
某重型变速箱工厂部署的虚拟装配平台:
通过激光扫描建立齿轮副数字模型
自动生成最优垫片组合方案
装配一次合格率从82%提升至98%
五、行业发展趋势与标准升级
根据AGMA 6006-A03最新修订草案,2025年起将强制要求:
行星齿轮轴向间隙检测采用动态测量法
定位精度等级新增Class 0级(误差≤0.005mm)
装配过程需记录完整的应力-应变曲线
当前,采用纳米级表面织构技术的定位端面处理工艺,已实现摩擦系数降低40%、抗微动磨损能力提升3倍的技术突破。随着人工智能技术在装配工艺中的深度应用,预计未来三年内齿轮定位精度可再提升50%。
通过上述技术创新与实践验证,减速机齿轮定位正从传统经验型工艺向数据驱动的精密工程转变。企业需建立全生命周期的精度管理体系,在材料科学、检测技术、智能控制等交叉领域持续投入,方能在高端装备制造领域建立核心竞争优势。