减速机用换油吗
来源:减速机知识 发布时间:2025-04-10 16:39:58 阅读:3864次
减速机润滑维护的核心:换油周期与科学方法解析在现代工业设备中,减速机作为动力传输的核心部件,其稳定运行直接影响生产效率与设备寿命。润滑油的更换作为减速机维护的关键环节,常引发用户疑问:是否必须定期换油?如何判断换油需求?本文将系统分析减速机润滑油的作用、失效规律及科学换油策略。
一、润滑油对减速机运行的关键作用
1. 降低机械磨损
减速机内部齿轮、轴承等运动部件在高速啮合时,表面接触压力可达数吨。润滑油形成的油膜能有效隔离金属直接接触,将摩擦系数降低70%以上。实验数据显示,润滑不良的减速机齿轮磨损速度是正常工况的5-8倍。
2. 控制运行温度
摩擦产生的热量通过油液循环传递至箱体散热。当油液氧化变质后,其导热性能下降20%-40%,导致设备温度异常升高。某水泥厂实测显示,油品劣化的减速机工作温度较正常状态高出12-18℃,加速密封件老化。
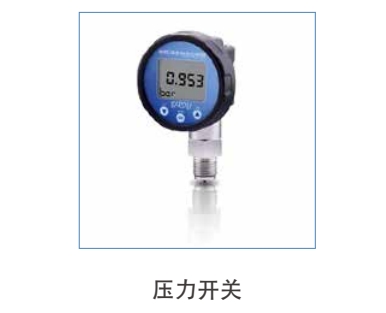
3. 防止腐蚀与污染
润滑油中的防锈添加剂可在金属表面形成保护层。若油液中混入水分(超过0.03%)或金属磨屑(含量>100ppm),将引发电化学腐蚀。某风电齿轮箱案例表明,污染物超标导致轴承点蚀,维修成本增加30万元。
二、润滑油性能劣化的典型特征
1. 理化指标变化
粘度异常:新油粘度波动超过初始值±15%需警惕
酸值上升:总酸值(TAN)超过1.5mgKOH/g时需更换
水分超标:Karl Fischer法检测含水量>500ppm即需处理
2. 微观结构改变
傅里叶红外光谱(FTIR)检测显示,氧化产物的特征峰在1740cm⁻¹处显著增强,表明基础油发生深度氧化。金属元素光谱分析中,铁(Fe)、铜(Cu)含量突增预示异常磨损。
3. 设备运行表征
异常振动值增加:轴向振动超过4.5mm/s(ISO 10816标准)
噪音频谱改变:高频段(>2kHz)能量占比提升20%以上
密封处渗漏:油品劣化导致橡胶密封件膨胀率超过12%
三、科学制定换油周期的三大依据
1. 制造商技术规范
主流品牌换油周期建议:
设备类型 |
初始换油期(小时) |
常规换油期(小时) |
摆线减速机 |
200-300 |
4000-5000 |
行星齿轮箱 |
500 |
8000-10000 |
蜗轮蜗杆减速机 |
300 |
3000-4000 |
2. 实际工况评估系数
重载(>额定载荷80%):周期缩短30%
高温(油温>90℃):周期缩短50%
多尘环境:增加油品检测频率至每月1次
3. 油液检测数据驱动
采用趋势分析法建立油品状态模型:当关键指标(粘度、水分、酸值)中有2项超过警戒值,或磨粒浓度进入异常磨损区(>50ppm),应立即换油。
四、规范化换油操作流程
1. 预处理阶段
设备停机后保持油温在40-50℃(利于杂质悬浮)
使用专用排油工具(如真空抽油机)清除95%以上旧油
箱体内部冲洗采用同型号新油,禁止使用柴油等溶剂
2. 关键控制点
注油量控制:油位应处于视窗的1/2-2/3处(静态时)
循环过滤:新油注入后空载运行30分钟,通过在线过滤器去除残留颗粒
密封检查:螺栓紧固扭矩需达到标准值的±5%范围内
3. 换油后验证
振动值下降率>40%为合格
油温稳定在(环境温度+35℃)±5℃区间
首次换油后500小时进行油样对比分析
五、润滑管理的技术升级方向
智能监测系统应用
在线粘度计、水分传感器与振动分析仪的集成,实现油液状态实时监控。某汽车生产线加装监测系统后,换油周期延长20%,维护成本降低15%。
合成润滑油普及
PAO合成油在高温下的氧化稳定性比矿物油提升3倍,某矿山设备使用合成油后,换油周期从2000小时延长至8000小时。
油品再生技术
离心分离+分子吸附工艺可使90%的废油恢复使用性能,某钢铁企业年处理废油300吨,节约成本超200万元。
润滑油如同减速机的"血液",其管理质量直接影响设备全生命周期成本。通过建立基于状态监测的润滑管理体系,企业可将非计划停机减少40%,延长设备使用寿命3-5年。在工业4.0背景下,融合物联网技术的智能润滑方案正在重塑设备维护范式。